Supply chain responsibility
Environmental, social, and governance (ESG) management across the value chain is crucial to Nornickel’s management culture. This focus ensures that the Company can convey its sustainability criteria to suppliers, involving them in its sustainability efforts. It also promotes standard‑compliant practices,address es relevant risks, and meets increasing consumer expectations. To bolster transparency in responsible supply chain practices, the Company publishes an annual Responsible Supply Chain ReportThe report is available on the Company’s official website..
GRI 2‑6
With an extensive range of by-laws, Nornickel is able to effectively mitigate the operational and financial risks and costs, reduce the working capital, make supplies more reliable, and improve the delivery cycle.
Nornickel’s by‑laws on the responsible supply chain
Key procurement by-laws
- Regulations on the Product Procurement Procedure for Nornickel Group Companies
- Procurement policies by category (group of similar products)
- A standard master agreement signed with every supplier
- Policy Regarding Support for Small and Medium Enterprises
- Efficiency improvement programme
- Responsible Sourcing Policy
- Supplier Code of Conduct
- Business Ethics Code
- Community Engagement Policy
- Occupational Health and Safety Policy
- Working Conditions PolicyAmong other things, this policy specifies working hours and rest periods, adopts zero tolerance to child and forced labour, and sets out the approach to remuneration.
- Indigenous Peoples’ Rights Policy
- Human Rights Policy
- Anti‑Corruption Policy
- Climate Change Policy
Nornickel has the Responsible Sourcing PolicyThe Policy is available on the Company’s official website. (the “Policy”) and its Supplier Code of ConductThe Code is available on the Company’s official website. (the “Code”) in place, which reflect the Company’s responsible sourcing principles.
Engagement with suppliers to build a responsible supply chain
Nornickel expects suppliers to meet the mandatory and target requirements and expectations set out in the Code.
To inform suppliers, the General Contracting Terms and Conditions, standard master agreement, and standard supplier contract forms were updated with a clause requiring compliance with the Company’s ESG requirements listed in the Code and the Policy. The clause also notifies suppliers that they can reach out to Nornickel’s Corporate Trust Line.
Contracts with suppliers were also updated to include an anti‑corruption clause:
- designed to ensure that contracting parties are on the same page as regards zero tolerance to corruption;
- obliging contracting parties to inform the other party in a timely manner about the identification of possible corruption risks and relevant checks;
- providing grounds for termination or other liability if the contractor violates the anti‑corruption clause and/or is involved in unlawful activities.
When assessing suppliers for adherence to the responsible supply chain principles, the Company categorises them as either mineral suppliersMineral suppliers in this section means suppliers, transporters, and processors of nickel-, cobalt-, and copper-containing minerals. or suppliers of goods, works, and services.
To monitor mineral suppliers’ compliance with the Code, Nornickel has a due diligence management system (DDMS) in place starting 2021. The DDMS focuses on compliance with the following requirements and guidelines:
- the Organisation for Economic Co‑operation and Development Due Diligence Guidance for Responsible Supply Chains of Minerals from Conflict‑Affected and High‑Risk Areas (OECD Guidance);
- the London Metal Exchange responsible sourcing requirements;
- the standards and principles of industry‑leading sustainability initiatives: ICMM, IRMA, RMI (including JDDS), as well as guidance from the China Chamber of Commerce of Metals, Minerals & Chemicals Importers & Exporters (CCCMC) regarding the due diligence process for responsible mineral supply chains;
- requirements of the Company’s major customers.
The DDMS focuses primarily on identifying potential risks that could affect the sustainability and transparency of mineral supply chain processes, and on minimising the risks listed in the OECD Guidance and covering the following areas:
- violations of human rights and freedoms;
- support for non‑state armed groups;
- illegal mine control and feedstock trafficking;
- corruption and bribery;
- misinformation across the supply chain from ore mining to product delivery to consumers.
DDMS tools make it possible to collect more data on participants along the mineral supply chain, including their environmental, social and corporate governance (ESG) practices.
To develop the DDMS, the Group’s divisions adopted standards for due diligence of mineral suppliers: in 2021–2022 relevant standards were approved by Polar Division, Kola MMC and Bystrinsky GOK, and in Q4 2023 by Medvezhy Ruchey. The standards govern due diligence of mineral suppliers, interactions between business units, and define the parties in charge and their responsibilities.
Since 2021, the Company has been conducting annual due diligence of mineral suppliers. In the reporting period, the exercise covered mineral suppliers of Polar Division, Medvezhy Ruchey, and Kola MMC. No due diligence took place at Bystrinsky GOK as it does not have any mineral suppliers. Following the due diligence of 100% of mineral suppliers for the Group’s Russian assets, no risks or risk indicators were detected.
Listing of Nornickel’s nickel, cobalt, and copper brands on the London Metal Exchange obliges the Company to submit RFARFA means Red Flag Assessment. reports starting from 2022. These reports confirm our adherence to the LME’s responsible supply chain requirements. The reports for 2022 were duly acknowledged by the LME in 2023.
In 2023, Nornickel extended its supplier assessment to cover suppliers of goods, works, and services, evaluating their compliance with the Code (including sustainability criteria). To this effect, the Company drafted a supplier self‑assessment questionnaire that includes ESG matters to appraise the sustainability practices of suppliers. Takeaways from a pilot with a sample group of suppliers are disclosed in the Responsible Supply Chain ReportThe report is available on the Company’s official website. for 2023.
Counterparty screening in procurement
As part of procurement activities in the reporting year, Nornickel conducted routine screening of both existing and potential counterparties. These checks focused on reliability, solvency, and financial health. The procurement process also comprises controls of conformity to sustainability criteria.
Sustainability factors
Ensuring procurement efficiency and transparency
Nornickel conducts all procurement via an automated supplier relationship management system – SAP SRM. By year‑end 2023, SAP SRM had been rolled out at 30 Russian business units and branches, with over 11,000 potential suppliers registered. Nornickel’s current and potential suppliers can communicate online with procurement teams for all categories of products purchased and receive up‑to‑date information regarding ongoing procurement. Sign‑up for the SAP SRM is free of charge and does not impose any obligations.
In addition, our website has a dedicated Suppliers section, which provides key information on the Group’s procurement principles and procedures and planned needs. The page also features announcements and invitations to participate in the Company’s tenders.
Product quality and supply reliability
Product quality assurance
Nornickel rigorously respects customer interests, assuring product quality by:
- complying with statutory requirements, contracts, standards, and regulations in product quality and distribution;
- managing risks that impact product and service compliance and capacity to enhance customer satisfaction;
- advancing production and technologies in line with sales and marketing strategies;
- prioritising the enhancement of customer satisfaction with product and service quality;
- ensuring that the quality management system aligns with leading international standards, promoting ongoing improvements and performance.
Product quality related goals and objectives are in line with the Company’s strategic goals and are formulated in the management’s resolutions based on annual performance reviews of the Corporate Integrated Management System.
Corporate Integrated Management System
Nornickel has a Corporate Integrated Management System (CIMS)Kola MMC has an integrated management system (IMS), which complies with ISO 9001:2015, ISO 14001:2015, and ISO 45001:2018., which is improved in line with international standards ISO 9001:2015, ISO 14001:2015, ISO 45001:2018.
The CIMS comprises a set of interrelated and interacting processes, activities, procedures, rules, organisational structure and resources required for achieving the Company’s goals and fulfilling the Company’s ambitions and commitments articulated by the senior management in the quality, environmental, occupational health and safety policies.
In 2023, a number of recertification and surveillance audits were conducted at Nornickel’s divisions. The audit confirmed CIMS compliance with ISO 9001, ISO 14001, ISO 45001 (for more details, please see the Certification of the Corporate Integrated Quality Management System appendix). The research centres and laboratories, which, as part of the Group, analyse the ore feedstock, semi‑products and saleable products, have quality management systems certified for compliance with GOST ISO/IEC 17025‑2019 General Requirements for the Competence of Testing and Calibration Laboratories.
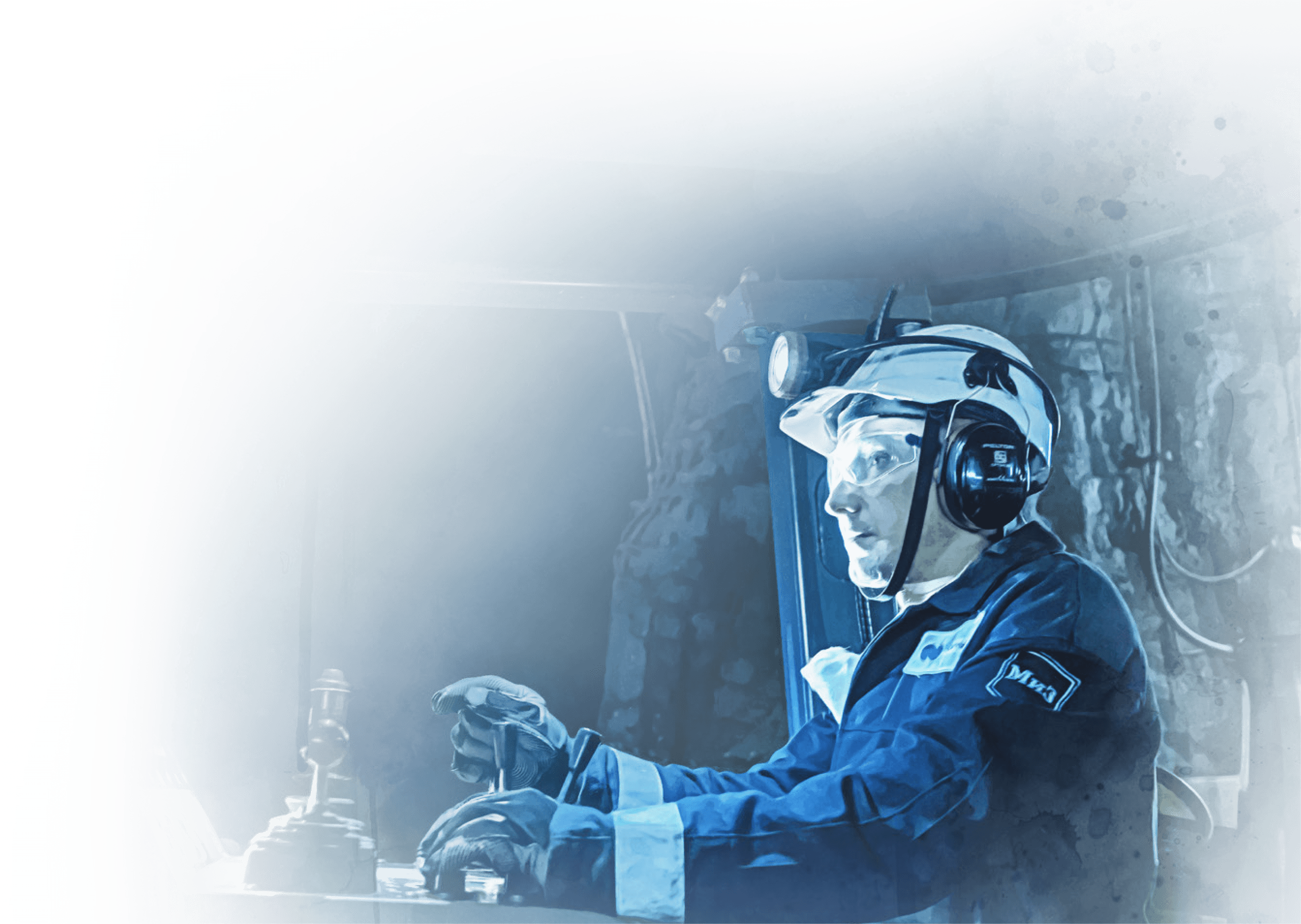
While Nornickel’s products are not subject to mandatory certification, the Company opts for voluntary certification by an independent third party to reaffirm compliance with the established standards.
The Company’s goods are labelled to keep the customers and carriers informed about key properties of the products (including those meant for exports). The labelling rules are set out in product‑specific regulations and take into account the GOST 14192‑96 (Cargo Labelling) requirements and contractual obligations.
Consumer properties of each product are defined in the relevant specifications and contractual documentation in full compliance with Russian and international laws.
Ensuring reliable and uninterrupted supplies
Nornickel’s sales strategy is focused on strengthening its positions in the market, with the Company seeking to achieve a balanced ratio of nickel supplies to stainless steel producers and other industries. As the largest palladium producer, Nornickel is implementing a strategy of direct long‑term contracts with its end users (with a focus on the automotive industry) in order to maintain a long‑term and sustainable demand for palladium.
Customer satisfaction
To enhance product quality and bolster customer loyalty, Nornickel conducts annual customer satisfaction surveys. Additionally, the Company routinely monitors and analyses the fulfilment of contractual obligations.
The key to positive survey results is maintaining or exceeding target customer satisfaction level at 2.50 points (out of 3 points). According to the 2023 survey, the customer satisfaction level stood at 2.87 points (up 0.7% y‑o‑y), which fully meets the target.
In 2023, the Company received 27 complaints and grievances about its product or service quality and achieved out of court settlement for all of them by meeting the demands of consumers. Out of the complaints received, 14 were deemed unfounded; however, the grievances and suggestions were considered. Corrective measures were formulated for 15 complaints, including two unsubstantiated ones.
To mitigate the risks affecting product quality and capacity to enhance customer satisfaction, the Company annually develops a comprehensive action plan to improve customer satisfaction.