Research and development
How has the trajectory of the Company’s R&D endeavours evolved over the past 20 years?
Nornickel embraces R&D and innovation efforts as the fundamental drivers of increased production, high product quality, and reduced environmental footprint. The Company was systematically building a substantial intellectual foundation by accumulating R&D assets, fostering relationships with research institutes, and nurturing corporate scientific expertise.
As Nornickel evolved, so did its goals and objectives. While the initial focus was on maximising the extraction of non‑ferrous and precious metals from ore and curtailing expenses, the emphasis has now shifted due to new environmental standards and production reconfiguration, which profoundly influenced process flow redistribution and technological re‑engineering. Today, designing cost‑efficient and effective technical solutions and diversifying Nornickel’s product range are front and centre.
Throughout these 20 years, the Company has conducted extensive R&D across multiple focus areas, established dedicated labs and research centres (including mobile environmental, forensic chemistry, and digital labs), brought to life over 2,000 employee‑driven improvement initiatives, and actively participated in numerous applied research conferences.
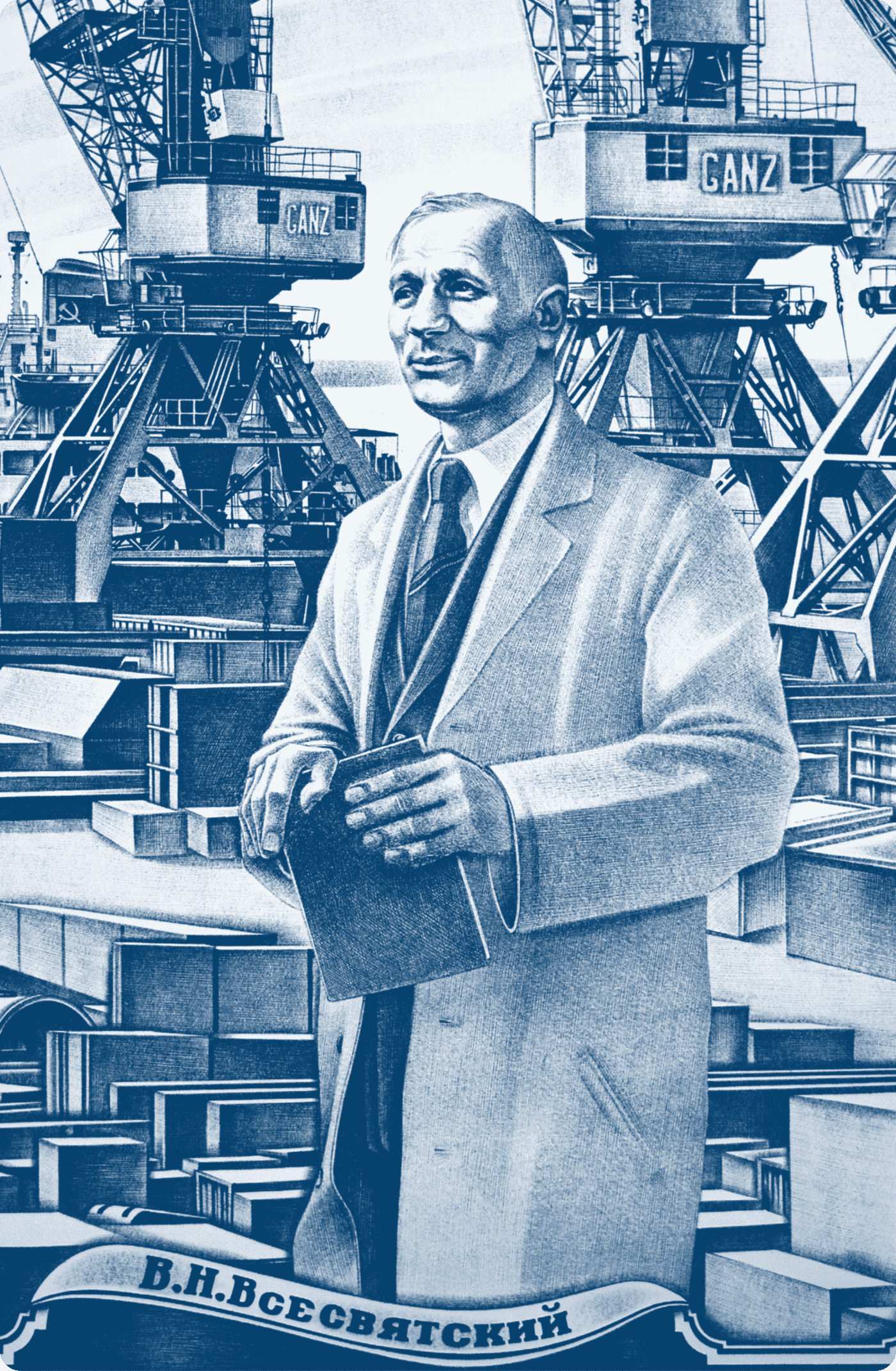
Nornickel’s contribution to the Science and Universities national project
Relevant UN SDGs
Related federal projects
Development of science and scientific‑and‑production cooperation
Development of advanced R&D infrastructure
Key initiatives and focus areas
Endeavours of Gipronickel Institute, Palladium Centre, and Nornickel Digital Lab
Support for graduates of vocational education institutions
Cooperation with universities to develop and test advanced technologies and train highly skilled staff
Development of cooperation with the Russian Academy of Sciences
Primary goals of Nornickel’s R&D efforts
Enhancing and advancing production processes
Diversifying the product portfolio
Providing technological support for operations
Ensuring technological sovereignty
Nornickel’s approach to R&D is guided by the principles enshrined in its R&D Management Policy.
The decision‑making process is supported by the R&D Council’s consultations and expert reviews.
In 2023, the Company pushed forward existing and commenced new R&D projects and feasibility studies seeking to amplify efficiency and environmental safety in production, complete major reconstruction and upgrade of production facilities, enhance concentration capacities, and bolster financial health.
Nornickel propels proprietary tech advancements primarily through the Group’s Gipronickel Institute, Palladium Centre, and Nornickel Digital Lab. Furthermore, the Company engages specialist engineering firms and leading Russian universities for research endeavours (under effective agreements with the Siberian Federal University, Fedorovsky Polar State University, and other scientific and academic institutions).
Gipronickel Institute
Gipronickel Institute, Nornickel’s principal research and design hub and one of Russia’s premier institutes for mining, concentration, metallurgy, and mineral processing, undertakes a vast array of services. These include designing eco‑friendly, high‑tech facilities, supporting construction, operation and manufacturing of saleable products, and information modelling for both Nornickel’s Russian business units and third parties in the metals and chemicals sectors.
The multifunctional engineering centre boasts four technology and two testing labs. In 2023, Gipronickel Institute established a dedicated lab focused on creating competitive domestic cathode materials (CAM) for lithium‑ion batteries. The team devised multiple production processes for CAM using nickel and cobalt sulphates and a precursor synthesis co‑precipitation method (PCAM), including CAM alternative production schemes (PCAM). The R&D activities helped produce market quality cathode materials equalling their commercial counterparts as certified by independent laboratories. A pilot batch of CAM was manufactured, with an end‑to‑end technology put in place that covers the lifecycle “feedstock – cathode material – recycling”. Battery recycling initiatives kicked off with preliminary lab tests that yielded high‑quality samples, paving the way for intellectual property registration (three patents pending). Looking ahead, the Company plans to produce high‑purity materials, specifically crystalline nickel and cobalt sulphates, along with advanced products like PCAM/CAM.
Moreover, in 2023, Gipronickel Institute identified prospective tech partners to advance concentration and metallurgical processing techniques within the scope of the Kolmozerskoye deposit development project. In 2024, Nornickel plans to develop a technology for extracting lithium from spodumene ore, with the first pilot batch expected in 2026.
In 2023, the Institute’s innovative solutions obtained international patent protection: the continuous converting technology – in South Africa, and the roast–leach–electrowin technology – in Kazakhstan and China. Applied in production, these technologies help tackle environmental challenges, conform to environmental laws, reduce the cost of end products, and enhance metal recovery for saleable productsFor more details on the technologies, please see the 2022 Sustainability Report..
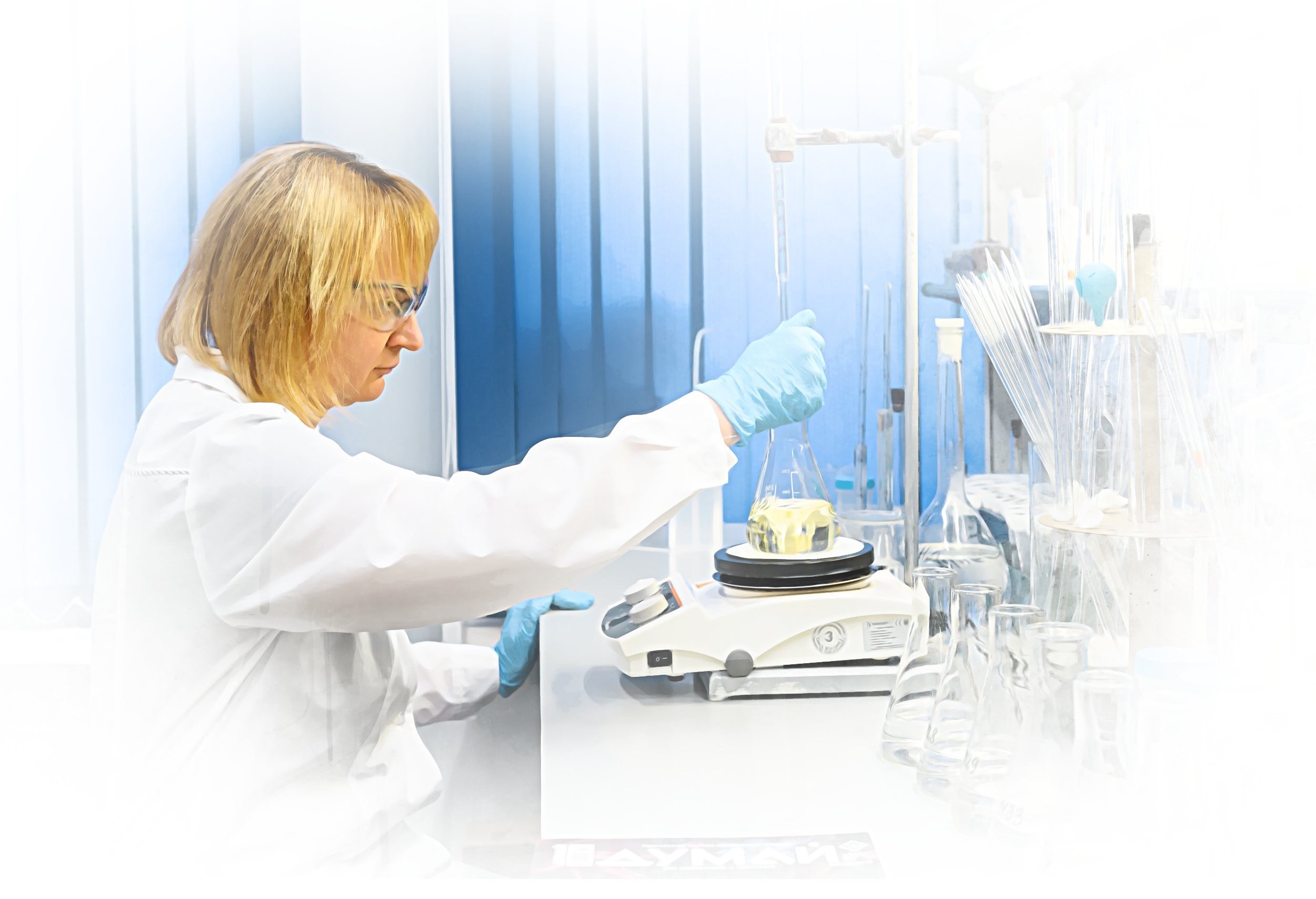
Palladium Centre
We also engage in R&D focused on palladium due to its significant role in fostering a green economy.
In most cases, palladium exhibits superior catalytic activity and high magnetic susceptibility, thereby bolstering the efficiency of technological processes. These properties broaden its utility across various industries, including hydrogen energy, chemical synthesis, and microelectronics. When mixed with other elements, it can manifest unique optical features that could amplify the performance of solar generators. Consequently, palladium‑based materials and alloys can improve cost efficiency and expedite the growth of several cutting‑edge industries.
Our current portfolio boasts over 20 products at different stages in the development pipeline, with 14 classified as ESG.
Palladium applications in hydrogen energy are extensive across the entire production chain: from hydrogen dissociation from water, extraction from gas, transportation, to its use in fuel cells.
In 2023, the Company:
- successfully produced catalyst samples for electrolysers that incorporate 30% replacement of iridium with palladium. These samples exhibit a threefold boost in performance in contrast to their commercial counterparts;
- synthesised fuel cell catalysts, where 25% of platinum is replaced by palladium, yielding more than a twofold performance hike versus commercial alternatives. Our target is to elevate this replacement level up to 80%.
These samples are currently undergoing validation by reputable overseas partners ahead of supplies to end users.
The Company is designing a cutting‑edge thin‑film solar panel cell based on palladium chalcogenide to enhance efficiency in comparison to the conventional silicon, tellurium, or copper based alternatives.
We are developing an array of products for novel chemistries such as catalysts conducive to synthesising glycolic acid for skincare use, FDCA acid for biodegradable packaging, and elements for the disinfection of water. The customer trial phase is slated for 2024.
In partnership with R&D institutes, fundamental research is underway to explore palladium’s prospective uses on a longer horizon – in superconductors, supercapacitors, microelectronics, spintronics, and even medical devices.
The Palladium Centre is actively forging a network of experts and customers, encompassing collaborative research with both domestic and international institutes and labs. This strategy includes engaging with potential customers in the Asia‑Pacific to reduce time to market for innovative products.
In the long run, the goal is to create over 100 new palladium‑based materials. Their deployment could spur at least 40 tonnes of new palladium demand by 2030The Company’s internal projections..
These projects and initiatives align with the goals of the Company’s Sustainable Social Development Strategy, fostering technological and social progress through Nornickel’s offerings, such as water purification systems using palladium, batteries for green transport, hydrogen energy solutions, and more.
With the Company’s support, my colleagues and I have developed and brought to life innovations that bolster sustainable practices within the roasting section of the Refining Shop and boost productivity.
For example, we successfully implemented a method of nickel electrowinning from chlorine dissolved tube furnace nickel powder in the Refining and Nickel Electrolysis shops. Another achievement was the launch of the Reducing Agent Transportation project, which helped us cut the Transport Shop’s costs.
Alexander Krasikov,
grade 5 roaster, Refining Shop, Kola MMC
(length of service with the Company — 33 years)
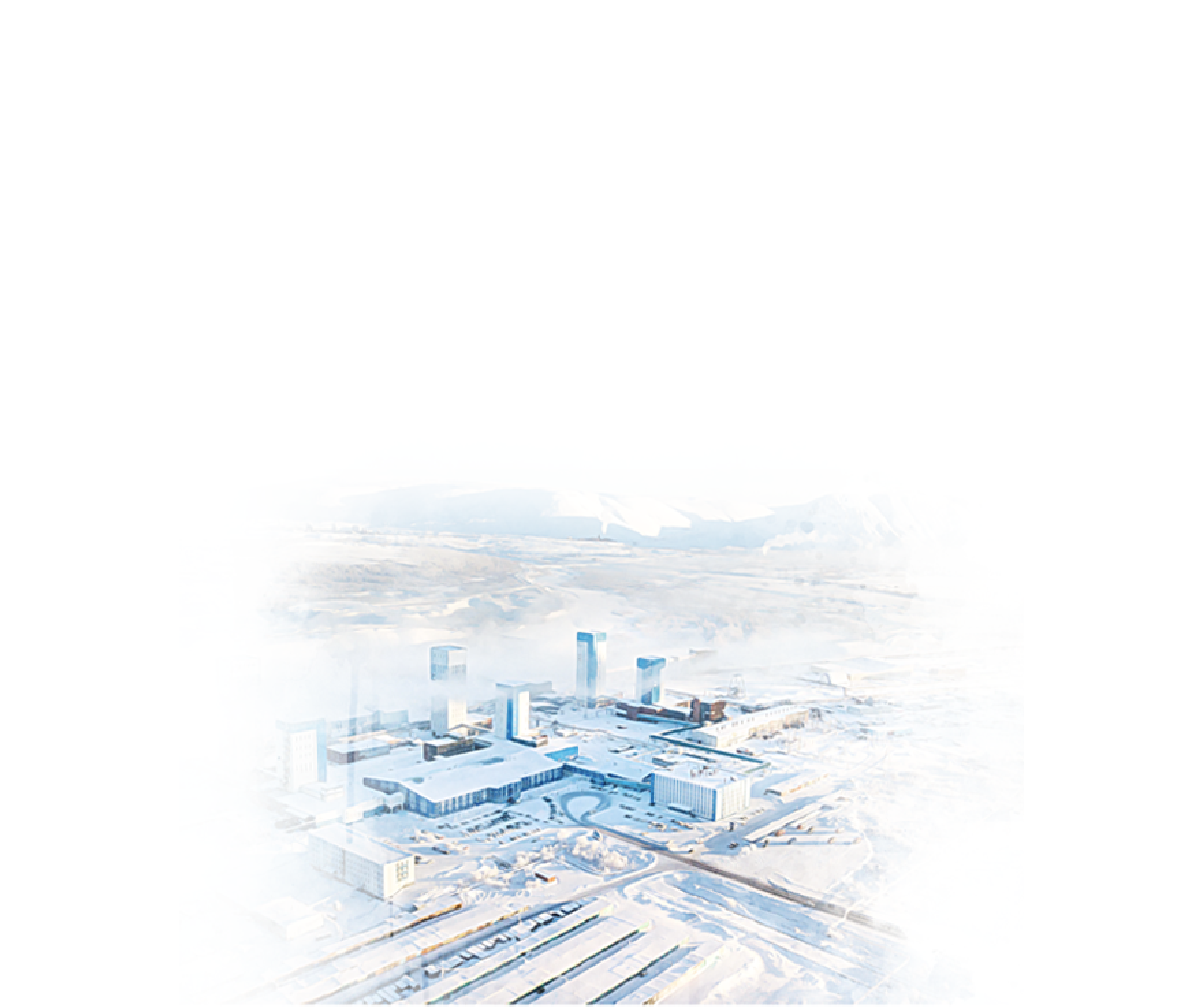